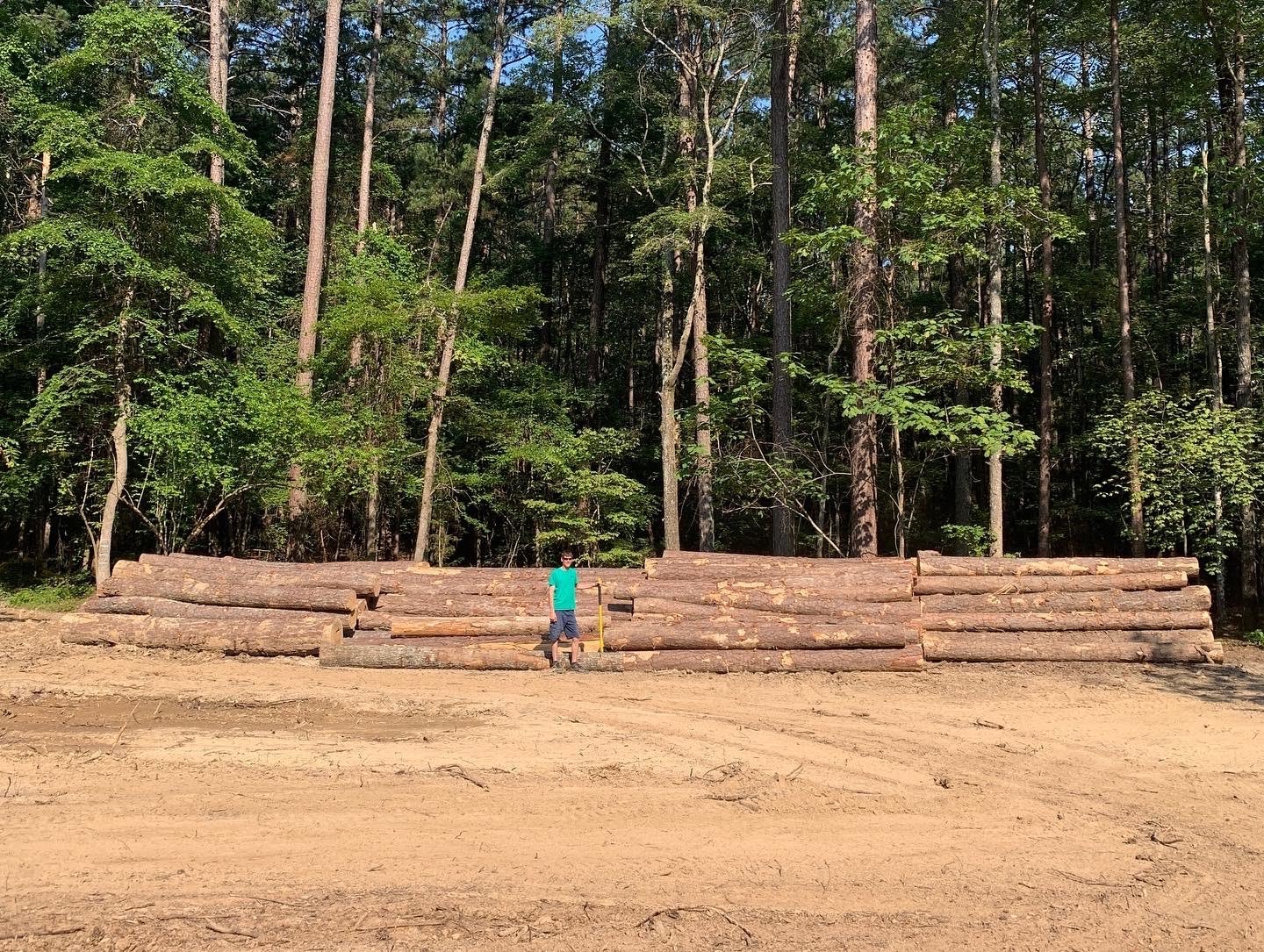
The 10-Step Challenge: How To Divert Logs From The Waste Stream To Become Affordable Homes
Introduction
The following 10-Step Challenge outlines the elements of an urban wood commodity chain. It provides a glimpse into some urban wood best practices— and it serves as the undergirding of the Triangle Urban Wood Utilization Program. It’s presented here as a challenge, rather than an existing network, because it is a prototype being built right now in the Durham-Chapel Hill area. To succeed, it needs the help of stakeholders— like you. The design is based on research findings from Vibrant Cities Lab and existing urban wood programs— most notably Baltimore’s Camp Small and Texas Urban Sawmill both of which got support from the U.S. Forest Service’s Wood Innovations Grant.
Compared to other urban wood programs, the unique feature of the Triangle Urban Wood Utilization Program is its focus on affordable housing materials. Many programs rightfully focus on high-R.O.I. live edge slabs. In Orange and Durham Counties, however, affordable housing is a critical issue as the median home exceeds $600,000. A person making minimum wage needs to work 112 hours per week to afford the average local mortgage. Any effort to offset housing costs and increase housing stock is eagerly needed.
This focus on affordable homes adds a layer of logistical and financial complexity to an already daunting challenge: how can an urban lumber company, without the efficiencies of scale of multi-million dollar enterprises, produce wood products that make homes less expensive? It’s possible, but it depends on a two things. First, we must identify niche wood products that can be made from local log supplies. These products must be manufactured efficiently with medium-scale sawmills, kilns, and workshops. See our Products Page for a deep dive into the niche products that fit this bill.
Second, all the stakeholders must understand the complexities of the whole urban wood system. It’s too big for one company or city to manage. Minor adjustments in one spot —arborists who cut longer log lengths, or builders who install mixed hardwood floors— can lead to opportunities throughout the commodity chain. Toward that end, here are the steps to a process that enables local trees to become affordable homes.
Step 1: Educate People About Urban Wood Waste
An estimated seven billion tons of urban wood waste enters U.S. landfills each year. Much of these logs could have become lumber for housing. Why didn’t they? In short, the system we have for processing lumber has made it more cost effective to cut large tracts, process in large facilities, and ship lumber around the globe than to utilize trees growing nearby. Much of the wood sold at nearby box stores comes from the Pacific Northwest, Canada, Romania, and other countries. One impact of this system is that local trees can’t efficiently enter the process and are often taken to landfills. There, they off-gas CO2 and methane, contributing to climate change as they decompose. It doesn’t have to be this way. A local urban wood commodity chain can decrease C02 emissions by sequestering carbon as building material. It can help everyone in the local wood-based business by creating jobs. And it can make local building materials less expensive and easier to access.
Step 2: Pass Legislation That Supports Local Lumber
The two biggest barriers to using urban lumber for home construction are (1) the efficiencies of scale that very large lumber manufacturers possess and (2) regulations that disincentivize local sawmills from producing construction lumber. Regarding the latter, in almost all cases, lumber used in code-approved construction requires a grade-stamp. This is a good thing as it ensures safety. However, the grade stamp process has become prohibitively expensive for local sawmills and includes site-specific criteria designed for multi-million dollar operations. Even if local sawmills can produce lumber superior to box store varieties, they can’t access the construction market due to these regulatory hurdles. In North Carolina, legislation like HB295: Promote NC Sawmills Act would level the playing field and enable small sawmills to institute quality control measures and sell grade-stamped lumber. Additionally, municipal and county “Highest Use” ordinances for urban wood can encourage builders to use local lumber.
Step 3: Work With Arborists Who Cut Sawlog Lengths
The critical first step in the urban wood commodity chain lies with the arborist. Professionals who remove urban trees rightfully prioritize safety for their crews and job-site efficiency. However, the industry practice of cutting logs into small firewood-sized rounds means that potential sawlogs get turned into unusable lenghts. This is especially the case with small-scale arborists who do not have equipment capable of handing sawlogs. Historically, every successful urban wood program has relied upon arborists willing to cut trees into longer lengths. It’s important to know that arborists often value drop sites that can take mixed-sized loads. When they clean up a site, whatever items are too big for their chipper, but too small to be a sawlog, need to get taken somewhere. An additional trip to a different site can be a make-or-break wager for arborists’ participation. Many urban wood programs include a firewood processing component to offer a community solution to this industry problem.
4. Utilize Commercial-Scale Log Pickups and Sort Yards
The key to getting a supply of usable urban sawlogs is to make it more cost effective for arborists and excavators. Even though there are now local wholesale log buyers, two barriers prevent arborists from selling them their saw logs. First, most of these wholesale buyers are far outside of town. Getting the logs to these lots require lots of time and costs to haul. Second, the prices for logs are now and will remain incredibly low. A pine sawlog, for example, sells for $35/ton locally. An arborist’s dump trailer may be able to carry $200 of material to the wholesale buyer but it may also take a half a day to deliver it. Wisely, the arborist would choose to dump the load for $40 at the local mulch-yard and take another $1800 half-day tree job. Any urban wood system needs convenient dump lots or to partner with a private sawmill business that offers free or low-cost commercial-scale log pick-ups.
5. Partner With High-Capacity Local Sawmills
Much of the literature about successful urban wood programs has rightfully focused on live-edge slab sales. The R.O.I. potential is huge: an inexpensive manual LT-15 Wide sawmill, run by one person, can produce many valuable live-edge slabs in a day. The limitation to these case studies, however, is that they depend on live-edge slabs being in demand. As the live-edge slab market gets saturated with DIY sawyers, and decreases in popularity among interior designers and woodworkers, it would benefit urban wood programs to consider a long-range Plan B. The construction market represents over 70% of all lumber sales in the U.S. And even if one species goes out of favor, another species will take its place. Trim, stair treads, porch railings, flooring, siding, framing lumber and more can provide urban wood processors with a steadier and larger market than slabs. The challenge to this scaling-up to construction materials, however, is that urban wood programs can no longer depend on small-capacity systems. Every part of the construction market requires larger scales: more logs, more sawmill thru-put, larger kilns, and the ability to move lumber by pallets.
6. Find and Use High-Volume Storage Areas
As consumers, builders value consistently high-quality products and easy commercial transactions. Unlike many DIY woodworkers, who may spend a day finding the perfect slab at the local sawmill, builders want to know the exact quantity a sawmill can deliver on a specific date. This poses a challenge to an urban wood business because its log supply can be more variable than a non-local box stores. Box stores can pull from international suppliers 24-7. A 100% local lumber company can address this in two ways: it can (1) limit its product offerings to those items that it can have in ready supply (eg, mixed hardwood flooring) or (2) stay stocked in inventory. Both of these strategies depend on having large areas for dry storage.
7. Dry and Process Lumber into High-Value Products
In the Durham-Chapel Hill area, rough-cut pine siding sells for $1.25/board foot. A 1x6x8, for example, sells for $5/board. If that board were kiln-dried and processed to become tongue and groove flooring, it would sell for $6/board foot, or $24/board. If it were processed into shou-sugi-ban siding, it would sell for $8.50/board foot, or $34/board. A successful urban wood business needs to understand ways to upsell, or add value, to its lumber. Although this involves heavy capital investment upfront —for a kiln, planer/moulder, etc.— the addition of millwork to an urban sawmill business ensures that it can produce specialty niche products to the local market. For the mission of affordable homes, this millworks aspect proves critical as the sawmill can produce specific items to offset the builder’s construction costs.
8. Establish Builder-Friendly Storage and Delivery Systems
When an urban wood business moves from slab sales to building materials, everything becomes heavier. Sales are no longer by the truckload; they now require trailers, forklifts, pallets, and flatbeds. Builders typically want two options: a place where they can send an employee to pick-up the lumber ASAP or a delivery to a jobsite. In both scenarios, palletized materials that can be moved by forklift or crane are preferable to hand loading. Because pine is a popular item in construction, local sawmills know the challenge of keep pine stain-free if milled in the humid North Carolina summers. Therefore, whatever facility processes urban pine for construction use has to ensure either immediate kiln-drying or sufficient airflow in well-designed storage sheds.
9: Partner With Builders Who Value Urban Wood
Veteran home builders often lament at the uncoordinated process by which many new homes come to the market. Subcontractors who don’t see the house as a whole system are more likely to do their work at the expense of another sub’s work: eg, the electrician runs a line on Monday where the plumber needs to drop in a drain on Tuesday. Furthermore, many builders are struggling with their inability to make a profit on small to medium-sized homes; therefore, they gravitate toward fancier homes just to make a profit. In this market of slim margins, builders are sometimes reluctant to use products or processes that require an extra step. Time is money. A wood business focused on the construction market must create products that play well with established workflows.
Step 10: Replenish Urban Trees
During the early 20th century, many cities planted urban trees without considering their native resiliences, needs, and lifespans. As a result, many of the urban canopy in the U.S. is reaching its peak maturity right now— and will continue to do so over the next 15 years. In N.C. many of these trees are Pin Oaks that are being taken down without consideration of how or where they are processed. (In Durham’s case, much of these oak logs head north to be buried in a private landfill). Once the trees are removed, they need to be replaced. Urban trees offer incredible value to citizens— from cleaning the air to cooling the heat island effect of inner cities.